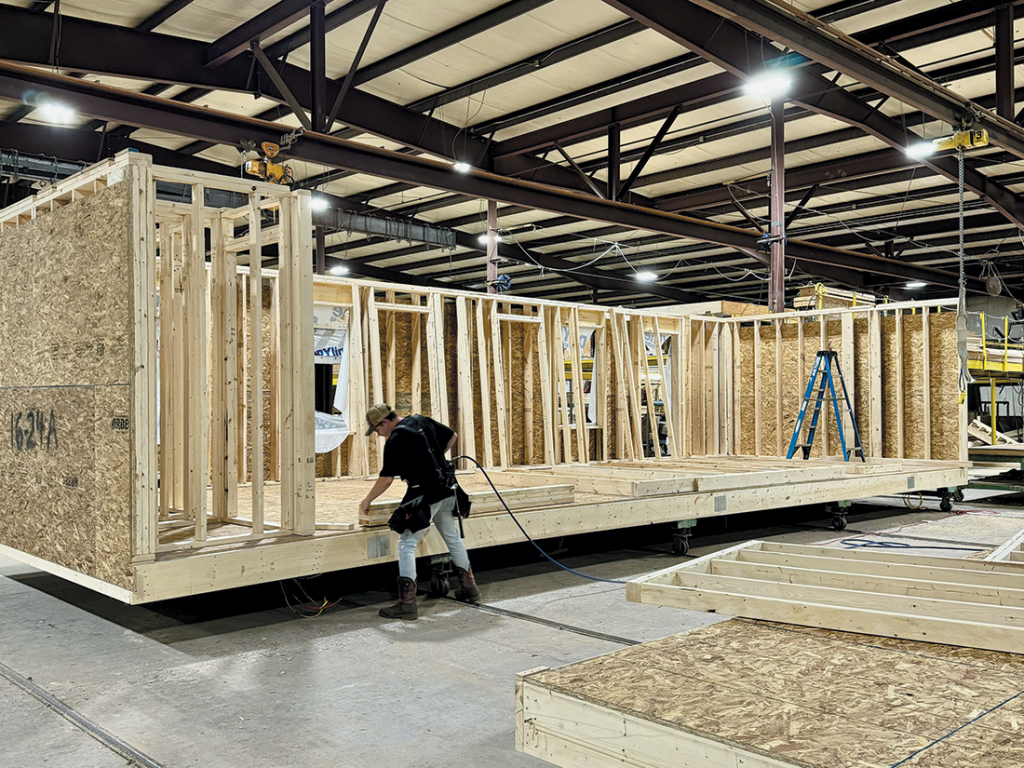
Courtesy Bill Lake Homes
By Susan Elise Campbell
Only 15 months since purchasing Bill Lake Homes, the new owners have started prepping an additional space for manufacturing the quality modular homes that the name “Bill Lake” has been associated with for more than 48 years.
“The modular world is fascinating,” said Jeff Knox, CEO and principal owner. Knox is a new construction residential/commercial developer who got his start buying and selling homes in the Albany-Saratoga area while a young man on Wall Street.
Partnering with Knox are his daughters, Katharine Pelletier and Abigail Sisson, son-in-law Garrett Sisson, and Christa Swistak, a non-family member. The team has a history of flipping homes together and builds modular homes on spec for residential developers, he said.
“Visiting factories in Pennsylvania showed me how quality modular homes, like the stick homes I built for decades the traditional way, can be constructed all year long indoors,” he said. “I always wanted to build my own manufacturing facility.”
“Our initial thought was to build a factory, but the team suggested, why don’t we see what’s out there,” he said.
Knox cold-called Bill Lake and asked if he might be interested in selling.
“We had a lot in common,” said Knox. “He gave me a price, I said it was fair, we shook hands, and closed in November of 2023.”
“Bill Lake has a phenomenal reputation for quality and loyalty,” said Katharine Pelletier, chief marketing officer and co-owner. “We have clients whose parents and grandparents bought a Bill Lake Home.”
For those unfamiliar with modular homes, Knox said many misunderstand the concept and think these structures are the same as mobile homes.
“The problem with 95 percent of modular home manufacturers is that they came out of the mobile home business,” he said. “They are selling mobile homes and modular homes on the same lot, so there is a marketing mindset that the two are the same.”
“There needs to be a better understanding of the distinct differences between the two products,” said Knox.
A modular home is like a mobile home only in the sense that it is portable and can be delivered just about anywhere. Specifications such as for framing and plumbing are unique to mobile homes and codes are different from a traditionally built home. Modulars are more comparable to stick homes in terms of the codes and standards to which they are built, according to Knox.
“Bill Lake was never a mobile home builder, he was a traditional builder who just thought he’d rather not be building out in the cold,” said Pelletier.
“What he did was set up a factory to essentially make the components of new houses indoors, where the materials and the crew are protected in a climate controlled environment,” she said.
“That is what we are continuing to do and why we kept the Bill Lake name,” Pelletier said. “There is a lot of equity in the name and an unmatched reputation for quality.”
“His method is to build a house the way he would if he were building on the lot, with attention to detail,” Knox said.
“That’s the one thing that impressed us and the one thing we told Bill we were not going to change,” he said. “I always regarded modular homes as stick homes built in a factory, and it’s just a better way to build a home.”
Knox and Pelletier said the company is committed to preserving the quality of the modular home product line. Upgrades such as granite or quartz countertops and higher grade cabinetry have become standard in all models. There are a few economy floor plans and new models are in the design phase now.
Pelletier is launching marketing and social media campaigns that appeal to the company’s targets, who are traditional residential builders and developers. Some 50 contacts connect to them from all over the Saratoga area and Capital District to collaborate on residential projects.
“Ours is a business to business model rather than selling direct to consumers,” Pelletier said.
But Knox added that most prospective home buyers come to Bill Lake Homes first, and then find a builder to prepare the lot and foundation and to partner with the modular company.
“Generally the end customer has land to put a home on but if not, and they are looking for a lot in this area, we can direct them to a broker at Sterling Real Estate Group,” Knox said.
Sterling Real Estate Group was started in 1999 by Jeff Knox and he remains the firm’s principal broker.
The partners have taken on 45 employees and a 140,000-square-foot manufacturing space. In the past year, the company fielded about 1,600 prospective buyer requests. Leads are still coming in from people who were raised in a Bill Lake Home or had a family member who owned one, Pelletier said.
There is a second structure on the property in Sprakers, NY that is close to 50,000 square feet and which Lake was using for personal storage. Pelletier said that has been cleaned out and will be dedicated to manufacturing.
With the added facility, the business will be able to deliver homes to an expanded geography. Knox and Pelletier said the market for their homes is strong because many models are in the 1,200 to 2,100 square foot range and modular construction affords some economies of scale unavailable to most developers.
For example, cabinetry, flooring, and countertops can be purchased in greater quantities and the savings passed on to the homebuyer, Pelletier said. With no disruptions due to weather, the time frame for building essentially 85 percent of the home indoors and completing it on site is reduced to only five or six months on average, versus 12 to 18 months for a stick house, Knox said. Inspections go faster, too.
Interested ones are encouraged to tour the facility at 188 Flanders Road in Sprakers, NY. Learn more at billlakehomes.com.