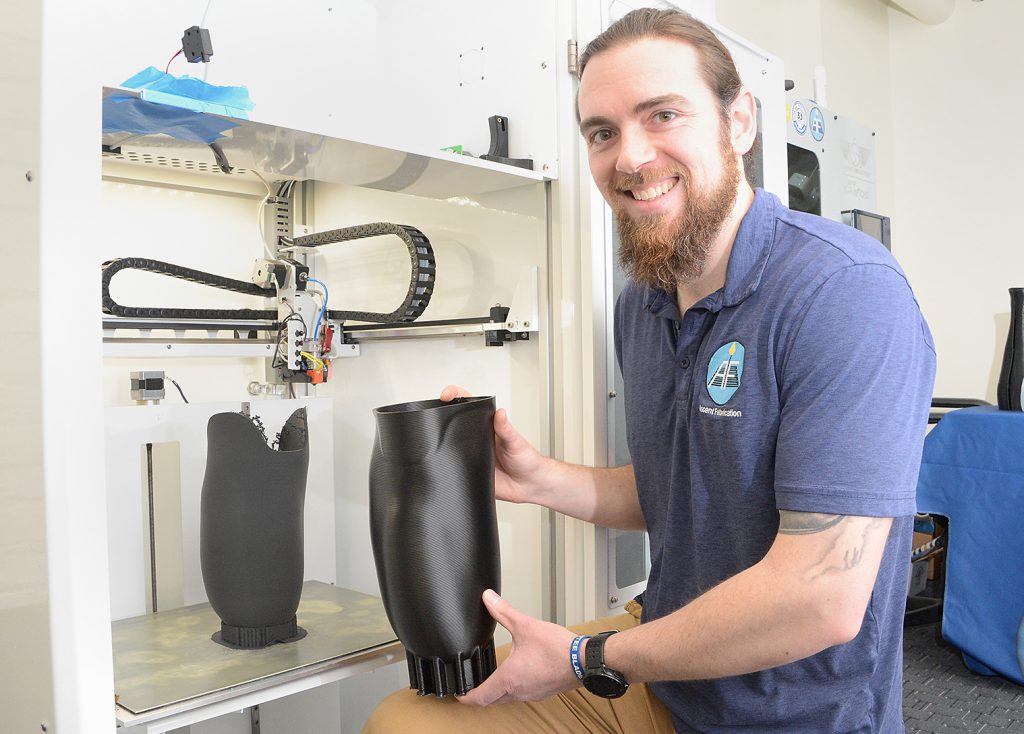
©2023 Saratoga Photographer.com
By Christine Graf
Certified prosthetist Joe Fairley has established himself as an innovator in the field of prosthetics and orthotics.
His company, Ascent Fabrication, utilizes CAD (computer-aided design) and 3D print technology to create highly functional and innovative prosthetic and orthotic devices.
Fairley developed an interest in CAD while a student at Saratoga Springs High School, and it was while pursuing a physics degree at Siena College that he taught himself how to use his department’s new 3D printer. After mastering the device, he established a group at Siena to create hero-themed, prosthetic hands for kids.
They partnered with e-NABLE, a global community of volunteers who use 3D printers to make free and low-cost prosthetic upper limb devices for children and adults in need.
It was through volunteering with e-NABLE that Fairley became interested in the clinical side of the field of prosthetics and orthotics. After working as a prosthetics technician at Sampson Prosthetics and Orthotics in Schenectady, he attended Northwestern University where he earned a M.S. in prosthetics and orthotics.
After graduating, Fairley began his residency at a clinic in Savannah, Ga., where the head clinician was a paralympic runner and founder of the nonprofit Amputee Blade Runners.
“I credit a lot of my clinical knowledge to him,” said Fairley. “He taught me to make running prosthesis, and I fell in love with working with high-activity patients.”
Fairley returned to Sampson in Schenectady to complete his orthotics residency, and while there, he focused heavily on 3D printing—technology that he had introduced to Sampson during the time he worked for the company as a technician.
“As we started to ramp up the 3D side of the business, we were getting requests from all over the country to teach other clinics how to 3D print and do CAD design,” he said. “We also started printing 3D devices for other clinics across the U.S.”
The process of creating a prosthetic or orthotic using a 3D printer begins with a 3D scan of a patient’s limb. The scan is then uploaded into CAD modification software where it can be clinically manipulated. After necessary modifications are made, the 3D printer is used to create the device.
In April 2021, Fairley established his own company, Ascent Fabrication, in order to focus on 3D printing of prosthetics and orthotics.
“I decided to go off on my own to better prepare the field as a whole to give them the educational tools they need to be able to implement 3D printing effectively in their clinic,” he said. “We provide a lot of on-site, in-house training, and I’ve flown out to six different clinics in the last eight months to teach them the exact process from start to finish. We also do a lot of virtual training and support.”
As its name implies, fabrication is at the core of Ascent Fabrication’s day-to-day operations.
“People can go on my web site and upload a 3D scan, and we can design a prosthetic or orthotic device to 3D print and ship out to them,” said Fairley.
Ascent Fabrication has grown exponentially over the past two years and is now headquartered at 480 Broadway in Saratoga Springs.
Ascent’s staff includes a 3D print technician as well as several contracted CAD designers. Fairley recently took on a partner in the San Francisco Bay area in order to expand the company’s printing capacities and reduce turnaround times and shipping costs.
According to Fairley, 3D printing is currently being utilized to create approximately 30 percent of prosthetic devices in the United States. He predicts this number will continue to grow.
“There will always be a reason to use some traditional techniques with hand casting on some of the more intimate parts of the body. But, I do think 3D printing is going to be the majority of how devices are made simply due to the increased efficiency and decreased cost of how we are providing these devices.”
In addition to offering fabrication of prosthetic and orthotic devices, Ascent Fabrication resells 3D printing filament plans. The company plans to begin its 3D printer leasing program in the near future. Ascent also partners with other companies to provide CAD design and 3D printing for applications outside of the prosthetics field.
As an example, Fairley said they are working with a local pool company to print 3D models of the different pools that the company offers.
“We can do practically anything marketing related,” said Fairley. “We can also do any kind of reverse engineering for any hard to find parts. We can really print just about anything.”
The business website is www.ascentfab.com.