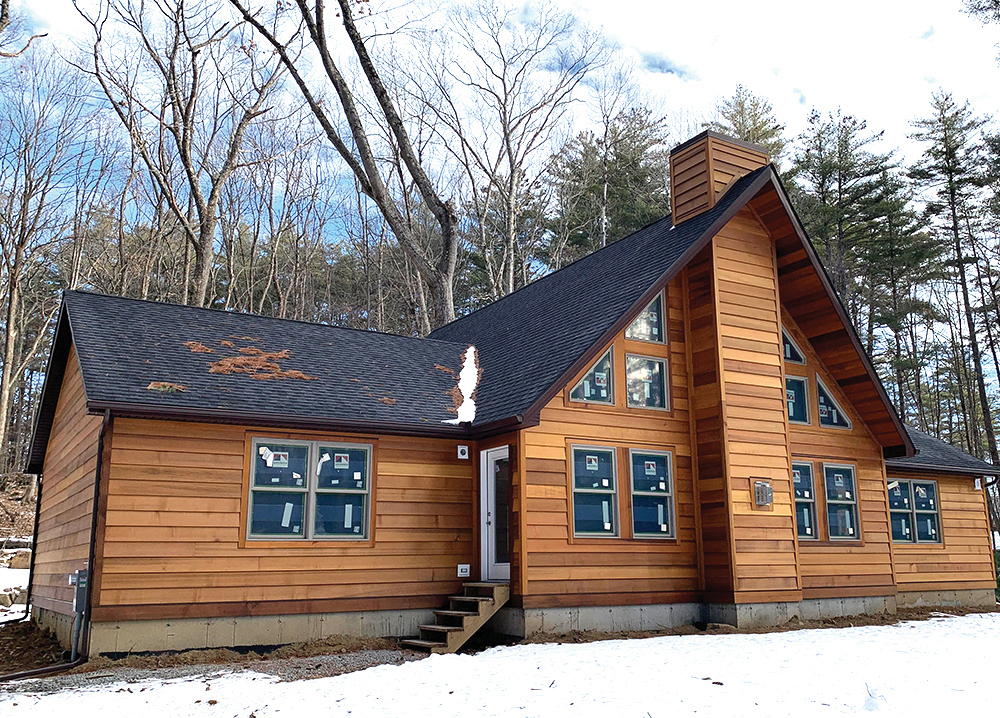
By Christine Graf
As demand for new homes surges throughout the country, supply shortages and price increases continue to plague the construction industry. According to the National Association of Homebuilders (NAHB), more than 90 percent of builders experienced materials shortages and delays in 2021.
Builders were encouraged when lumber prices began to fall after a record high in May of 2021, but prices began to climb again in December. The average cost of lumber is now about three times more than it was before the pandemic, industry officials say.
Economists predicted that supply chain shortages and material costs would begin to ease, but that was before Russia invaded Ukraine. Experts say the war in Ukraine will disrupt supply chains and further exacerbate shortages and price increases. The increase in oil and gas prices that have resulted from Russian sanctions will also impact production and transportation costs.
According to Cecil Provost, owner of Saratoga Construction and Saratoga Modular Homes, increased material costs have caused the average home price to skyrocket.
His companies build custom “stick-built” homes as well as custom modular homes. Stick-built homes are constructed on the job site, whereas modular homes are built in sections at a factory.
“Our specialty is building custom homes with modular construction. We are typically doing porches, and garages, and decks, and higher end finishes. What’s unusual about us is that we design every home from scratch for the customer. We can customize it right down to the bathroom faucets. We are the only builder that I know of in this region and one of the few in the northeast that do what we do.”
In the past 12 months, Provost said new home prices have increased more than 20 percent. Over the course of the last two years, they have increased as much as 35 percent.
“It’s significant, and the lead times are just brutal,” he said.
Modular home lead times have increased from eight to 10 weeks to five months or more. Some modular home factories are already totally booked for the entire year.
“A big advantage of the modular home construction is that once I order the home, that price is locked in,” said Provost. “Whereas if I get a price quote on a house worth of lumber, the quote is only good until 5:00, and it might be different tomorrow. There’s so much volatility out there right now.”
Building material lead times vary significantly by product. For example, Provost said the lead time on Andersen Windows has increased from three weeks to between 12 and 39 weeks. Garage doors have a lead time of four to five months, and kitchen cabinets have a lead time of up to six months.
“Some things are starting to ease up a little,” he said. “Last summer and fall, there was a real difficulty getting any premium colors of vinyl siding. A lot of the darker colors that are popular were temporarily discontinued. That’s starting to ease up, but there are still challenges out there, and it sounds like we have another year of this in front of us.”
The material shortage has resulted from multiple factors that extend beyond the pandemic shutdown that took place at the beginning of the pandemic.
“A lot of the products or raw materials needed to make the products come from overseas. And even if they are local, there is an enormous shortage of truckers to make deliveries,” said Provost. “The resin shortage originated from the ice storms in Texas a year ago. They shut down some of their refineries, and that caused a huge shortage of resin for vinyl siding and anything that had plastic in it. There are still trickle-down effects from that.”
Because of the long lead times and unpredictable product availability, estimating project completion dates has proved to be very difficult.
For the consumer, the cost of building a new home continues to rise. Surprisingly, the dramatic price increases have not impacted demand.
Provost said he is turning away potential buyers almost every day.
“Our demand is completely off the charts in the last 12 months, and I don’t see any end in sight,” he said. “A lot of that has to do with the strength of the economy in the Capital District. Industry wide, there is such a shortage of new construction and there has been for years. And now there is a shortage of labor as well. Finding labor is an enormous challenge.”
Before COVID, his company was building between 16 to 18 homes a year. Demand has increased dramatically, fueled in part by high demand for vacation and lake front homes.
“I could probably sell 50 this year, but I don’t think we are prepared to make that big of a jump,” said Provost. “We will probably build 30 this year, and we’re turning away millions of dollars a month. We have a waiting list into the middle of next year, and we’ve turned away more jobs than we’ve taken. It’s just crazy.”