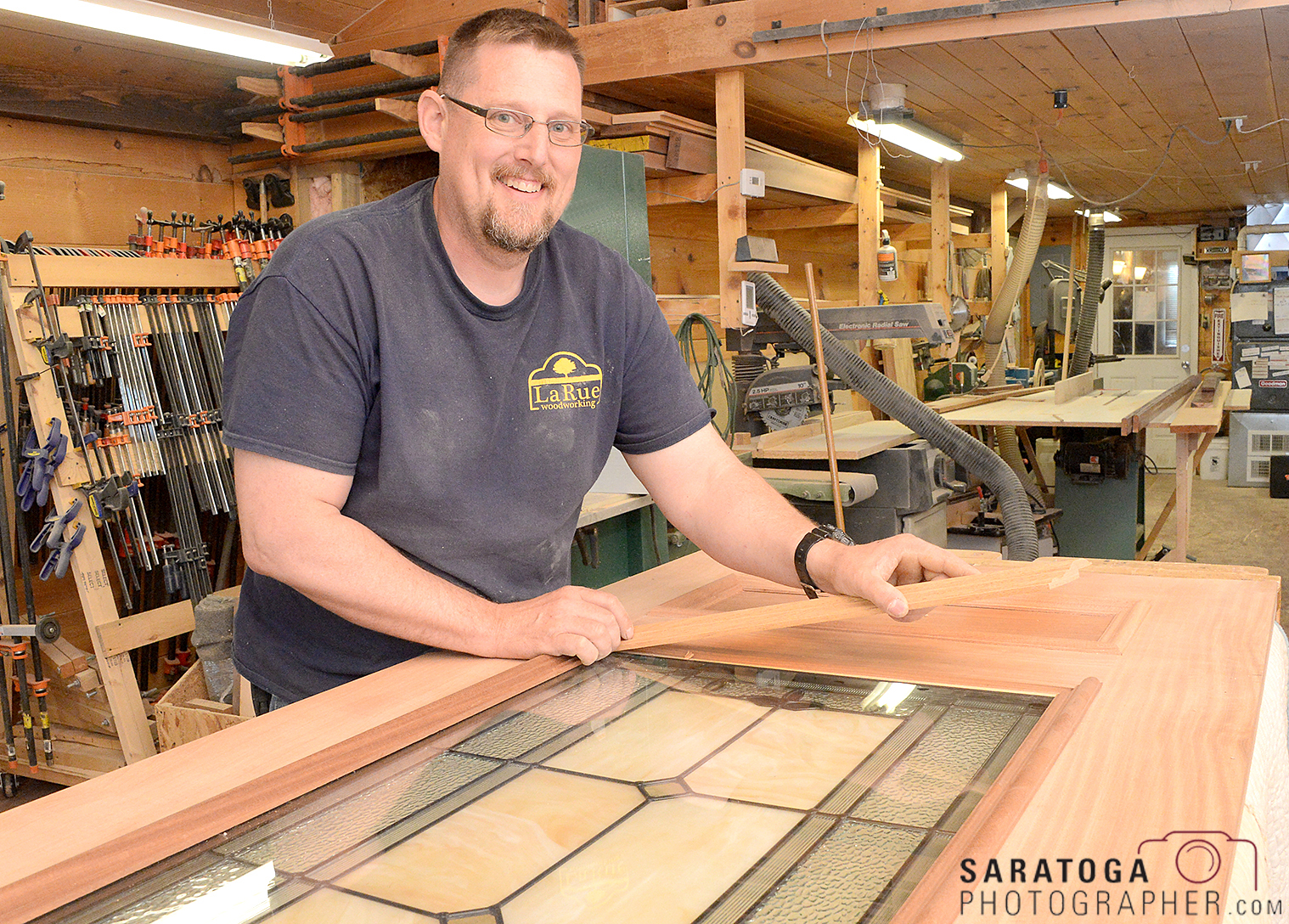
By Maureen Werther
Master craftsman Will LaRue has operated LaRue Woodworking (part of LaRue Enterprises) on his family farm for nearly 20 years and he continues to expand.
His most recent expansion of business comes in the form of a relationship with Curtis Lumber, an area business with its own history of longevity in the region. LaRue said that he is currently doing custom moldings, custom millwork, wood countertops through Curtis.
“They pretty much send over anything wood-related,” said LaRue.
His business is now running extra shifts. He has also hired two veterans, both former Marines, as well as his mother and his 17-year old daughter, Crystal, who handle the bookkeeping, website and social media.
LaRue is the seventh generation and his daughter is the eighth generation to occupy the farm at 621 Charlton Road, Ballston Spa. It is registered as a “national bicentennial farm” and continues to be a working farm, supplying hay and small grain to customers throughout the region.
LaRue began his career as a woodworker in the 1980s at the age of 8, and he vividly recalls selling his handmade cutting boards to the ladies at his church. His “big break” came in 2000 when he displayed what he calls “the bed” at the annual Woodworkers’ Showcase held at the Saratoga Springs Civic Center.
“Everyone loved it,” said LaRue He attributes the subsequent flow of orders to that initial exposure.
LaRue Woodworking quickly outgrew the original 900-square-foot workshop he built in the attic of the farm It now encompasses more than 10,000 square feet, which includes the main shop, a lumber storage barn, two sawmills, a drying kiln and another smaller woodworking shop.
The cutting boards LaRue mastered at the age of 8 are now being shipped by the dozens to a chic housewares boutique in southern California. This is not the first West Coast order for LaRue Enterprises. He said his business is drawing customers from around the country—Florida, Maine, Massachusetts and across the border in Canada.
LaRue makes everything from cutting boards to cupboards, bedroom furniture to bookcases, replicas of old sleighs to Model T replicas. He is also responsible for building the intricately ornate steeple that rests atop the Charlton Presbyterian Freehold Church. He crafted it entirely by hand.
LaRue’s ability to create furniture, cabinetry and accessories in a broad range of styles is part of what makes him sought after. Customers visiting his workshop can see firsthand examples and photographs of work he has done for customers ranging in style from contemporary and modern to rustic farmhouse and everything in between.
He is also a master repairman and a big percentage of his business comes from repairing antiques or furniture that has sentimental value for its owners.
He does warn his customers: “If you’re in a big hurry and want it tomorrow, I am not the person you want to work with.” However, he noted, once people visit his shop and see photos and real-life examples of his craftsmanship, they usually end up becoming customers.
LaRue also designs and builds many of the tools of his trade, including a surfacing table and flooring machines.
LaRue employs a more traditional method to track his workflow, progress and schedule. He depends on a simple, yet effective, flow chart in the form of a cork board and index cards. He said that the board keeps him focused on the number and size of his projects, as well as projected completion times.
LaRue’s newest employees, Bryce Tyrell and Katia Uveges, have been learning on the job for the past year. They said while LaRue is a perfectionist, he is also a great boss. They love what they do and appreciate learning a craft that allows them to transform a piece of reclaimed wood or the lumber from a felled tree into something useful, functional and beautiful.