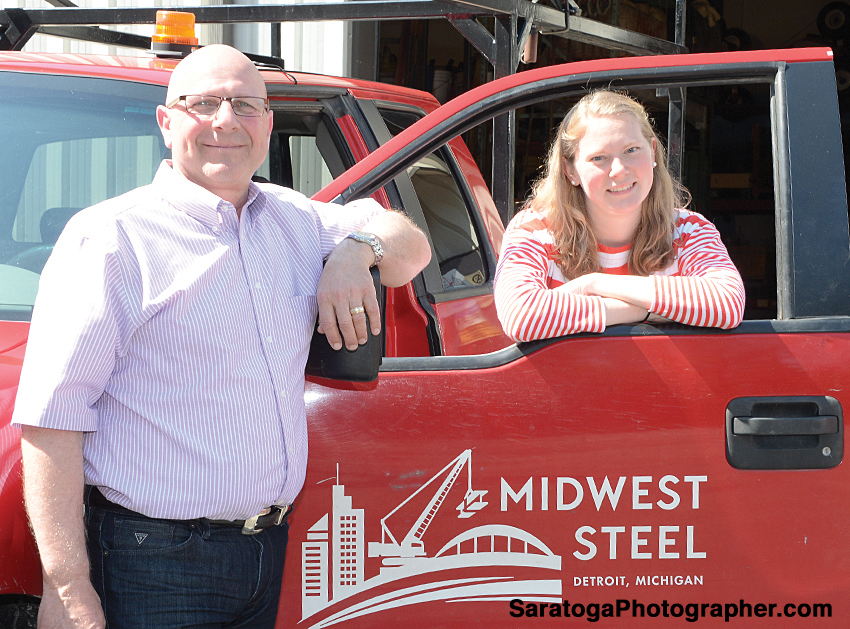
©2017 Saratoga Photographer.com
By Susan E. Campbell
The structural steel contracting industry is going so strong that one area professional foresees excellent employment opportunities for skilled ironworkers in the next few years.
Dino B. Benedict is the New York business manager for Midwest Steel. Headquartered in Detroit, the firm also has offices in Muncie, Ind., Orlando, Fla., and Ballston Spa.
In Saratoga County, it’s common to see a bridge, stadium, airport or other structures where Midwest Steel played a role in steel construction, precast concrete, or both.
“It is not typical in the industry for a company that erects the steel skeleton of a building to also form the concrete slabs that enclose that skeleton,” said Benedict.
Benedict said that some local projects include Samaritan Hospital, Rivers Casino, the ZEN building at SUNY Polytech, and GlobalFoundries. Business growth is so healthy in New York and the New England states that he predicts a shortage of welders, steel workers and other qualified laborers soon.
“It is a great time for young people out of high school to contact local unions about apprenticeship programs,” he said.
Whenever Midwest Steel takes on a project in the U.S. or Canada, the first step is for the project supervisor to meet with local union officials to discuss the scope of the project and manpower needs.
Similar companies rarely travel outside their immediate geographic area. But Midwest Steel has strong ties with all the local unions in the states and across the northern border, he said. This means that if the project is so big that local labor alone cannot meet the needs, the project supervisor will contact other unions for help.
“In other situations there may be a need for a special type of weld or a particular skill not available locally,” said Benedict. “We can send in workers from anywhere to fill that need.”
“The union halls are fully aware and involved with staffing and we have incredible relationships with them,” said Benedict. “We meet often about what we can do to help train the labor force, especially if there is a specific requirement for a project coming up.”
Founded in 1968 and family owned, Midwest Steel boasts a longevity also atypical in the industry. Benedict credits the values of the owners, Gary Broad, president, and his son Tom, executive vice president, as well as a loyal and skilled project management staff.
The company has low turnover. Benedict himself has been with Midwest Steel for 18 years, the last seven in Ballston Spa. The firm also has an experience modification rate (EMR), which gauges past cost of injuries and future chances of risk, that “at 0.061 holds the industry standard,” according to Benedict.
While an EMR of 1.0 is considered neutral, that measure would be considered higher for some industries and lower for others. EMR is specific to a company and primarily helps it measure performance against itself over time.
“The owners insist that everyone is well trained and safe, while achieving productivity and erecting buildings competitively,” he said. “It is a matter of business integrity that we treat our customers with respect and provide them good service.”
Benedict said high-tech building information modeling (BIM) programs are used to ensure that a material called for in the plan is actually being used, or to verify the right amount of welds, as well as many other checks and balances.
“BIM software allows us to construct the 3-D image of an entire building in real time,” said Benedict. “We can even crop in cranes and materials to assess logistics and other dynamic information about the structure.”
There is one quality control professional that visits all sites once or twice a week. This individual is certified to verify the quality of welds and bolting, often relying on the BIM software. Midwest Steel also hires third-party inspectors from the area as required.
Between the local union members and inspectors, there could be 100 or more jobs filled for any one project, according to Benedict.
“Steel construction is inherently dangerous and physical,” he said. “Using safety equipment reduces the danger ratio considerably, which is why it’s so important that we thoroughly train our workers.”
As the demand for skilled union ironworkers grows, Benedict encourages seeking out an apprenticeship, which is typically a three- to four-year program. Applying can be an arduous process. But Benedict said an individual can be put on a job as permit-status until the program begins.
For more information, visit www.midweststeel.com.