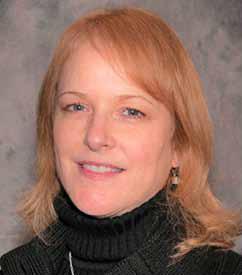
By Margie Miler
The good news is that residential construction
is coming back to life after one of the worst
downturns since the Great Depression.
It is no secret that a robust housing industry
is a leading indicator of a healthy economy. As
a share of the national economy, the residential
construction industry has historically played a
significant role, averaging almost 5 percent of
U.S. GDP, before the recession.
Residential investments (new construction, remodeling and equipment installation) contribute to other economic activities well beyond the construction trades, including housing finance and mortgage transactions; building material suppliers and manufacturers; utilities and services; and appliance and furniture purchases.
All of these account for approximately 15-20 percent of U.S. GDP, according to a recent Housing Committee report.
With anticipated housing starts of 970,000 this year and 1.18 million in 2014, the indicators are there for a gradual rebound in the market, and as the economy improves, a pent-up demand for housing is expected to increase.
Can there be a downside to a revitalization of an industry that is the backbone of our economy? There are so many industries connected to the home building sector that are finally breathing a bit easier and are now looking to hire additional staff.
Therein lies the rub. Residential construction stands out as one the few sectors where demand for new workers is rising, and yet there are increasing concerns from builders about the supply of experienced tradespeople now that demand for new homes is improving.
A growing labor shortage is just another hurdle for a fragile housing industry that is struggling to recover, and it can hurt overall economic growth. In some states that were hit the hardest by the housing crash, these shortfalls are slowing a much needed recovery.
As the economy mends, pent-up demand for housing will continue to grow to near normal levels of 1.7 million units annually. All construction spending, including commercial and government, is up more than 14 percent from the market bottom in February 2011, and yet construction payrolls remain virtually unchanged from two years ago, at 5.5 million. “Contractors are coping with the added workload in part by paying employees more overtime,” says Ken Simonson, chief economist of Associated General Contractors of America.
Labor Department figures show that the jobless rate has dropped from 17.3 percent to 11.4 percent the past two years, despite the industry’s static employment, as 320,000 construction laborers stopped working or looking for work.
In fact, all up and down the supply chain, a labor shortage has affected material supply chains and distribution networks that were disrupted when the market collapse hit. Lumber mills and other building product manufacturers looking to increase their production capacity are now struggling to replace workers that were laid off when building demand plummeted.
An estimated 1.4 million housing related jobs simply disappeared as a result of the recent housing boom collapse, causing many workers to seek other types of employment, and only a percentage of them will be returning to the field.
“What used to be high-paying, skilled jobs vanished as builders across the nation went out of business or were forced to let workers go,” said Rick Judson, NAHB chairman, a home builder from Charlotte, N.C. Some laid-off construction workers are trickling back as activity picks up, but others have become entrenched in other lines of work.
At a time when Baby Boomers are retiring and most high school graduates are steered towards college or high tech fields, even a moderate increase in construction activity contributes to an ever-widening gap between the supply and demand for construction labor.
“The survey of our members shows that since June of 2012, residential construction firms are reporting an increasing number of shortages in all aspects of the industry – from carpenters, excavators, framers, roofers and plumbers, to bricklayers, HVAC, building maintenance managers and weatherization workers,” said NAHB Chief Economist David Crowe. “I have heard many reports from builders who say they can’t hire enough people, they can’t find subcontractors, they’re unable to get the labor necessary to build homes that they do have on order — even at the low level of building that’s occurring right now.”
This is not bad news for skilled workers who may be able to command higher wages as demand for their services ramps up, but the impact of higher labor costs may be reflected in increased home prices or a reduction in construction activity. More than 50 percent of the builders surveyed by NAHB say they have had to increase wages or bids to secure workers, and 46 percent say the shortage has caused them to delay completing projects while 15 percent said they have had to refuse some work. Meanwhile, new homebuilding has reached its highest level of activity in four and a half years.
With many high schools scaling back their vocational training, especially with the recent years of budget cuts, there is a question of where this critical workforce will come from. Could our education system be doing more to address the needs of such an important segment of our communities’ economic well-being? Is the best solution to open our borders and welcome an influx of foreign workers, or to steer a portion of high school students towards blue-collar training that can lead to productive careers? Could we do better with those students who clearly aren’t academically inclined and who aren’t interested in obtaining a college degree?
Some in the industry feel that because of a cultural and political bias in favor of sending all kids to college, that there’s a stigma against blue-collar work, even though, in regards to earnings, construction work has historically provided stable wages comparable to those in manufacturing, and higher than many service sector jobs. Recently, almost all residential construction workers’ wages have stabilized nationally after declining during the downturn.
U.S. Labor Department figures show that there were 5,453 construction apprenticeship programs overseen by the federal government in fiscal 2012, down from 6,076 in fiscal 2007. It can take one to three years for an apprentice to be truly productive and there is a declining number of building related employers that are able to provide training, “Many commercial contractors offer apprenticeships and courses in-house or through trade groups and unions,” said Don Whyte, president of the National Center for Construction Education and Research. Such training is less prevalent than it used to be, however.
Contractors are reluctant to train workers that may be poached by their competitors in a hot labor market, and even if they are willing to train, their immediate need may require that they hire experienced trades people who can hit the job site and go to work the first day.
There is a growing need for professional contractors and well trained mechanics because of the complexity of some of the building projects.
There is ever advancing technology in the industry for things such as energy efficiency as well as for the installation of specialty products and equipment.
Even though many television shows make construction look easy, the reality is that it takes many years of hands-on experience to become proficient in the trades. Construction truly isn’t something that anyone can just pick up and perform to industry standards, and requires an investment in training. It is a worthwhile investment for our communities and our country.
Margie Miller works in sales and business development at Curtis Lumber in Ballston Spa.
Photo Courtesy of Curtis Lumber